Diseñoengranajes cónicosEl diseño de engranajes cónicos para entornos marinos implica varias consideraciones críticas para garantizar su resistencia a las duras condiciones del mar, como la exposición al agua salada, la humedad, las fluctuaciones de temperatura y las cargas dinámicas experimentadas durante su funcionamiento. A continuación, se presenta un resumen del proceso de diseño de engranajes cónicos para aplicaciones marinas.
1. **Selección del material del engranaje cónico**: CElija materiales resistentes a la corrosión, como aceros inoxidables o materiales con recubrimientos protectores.Tenga en cuenta la resistencia y la resistencia a la fatiga de los materiales, ya que los engranajes marinos pueden experimentar cargas elevadas y tensiones cíclicas.
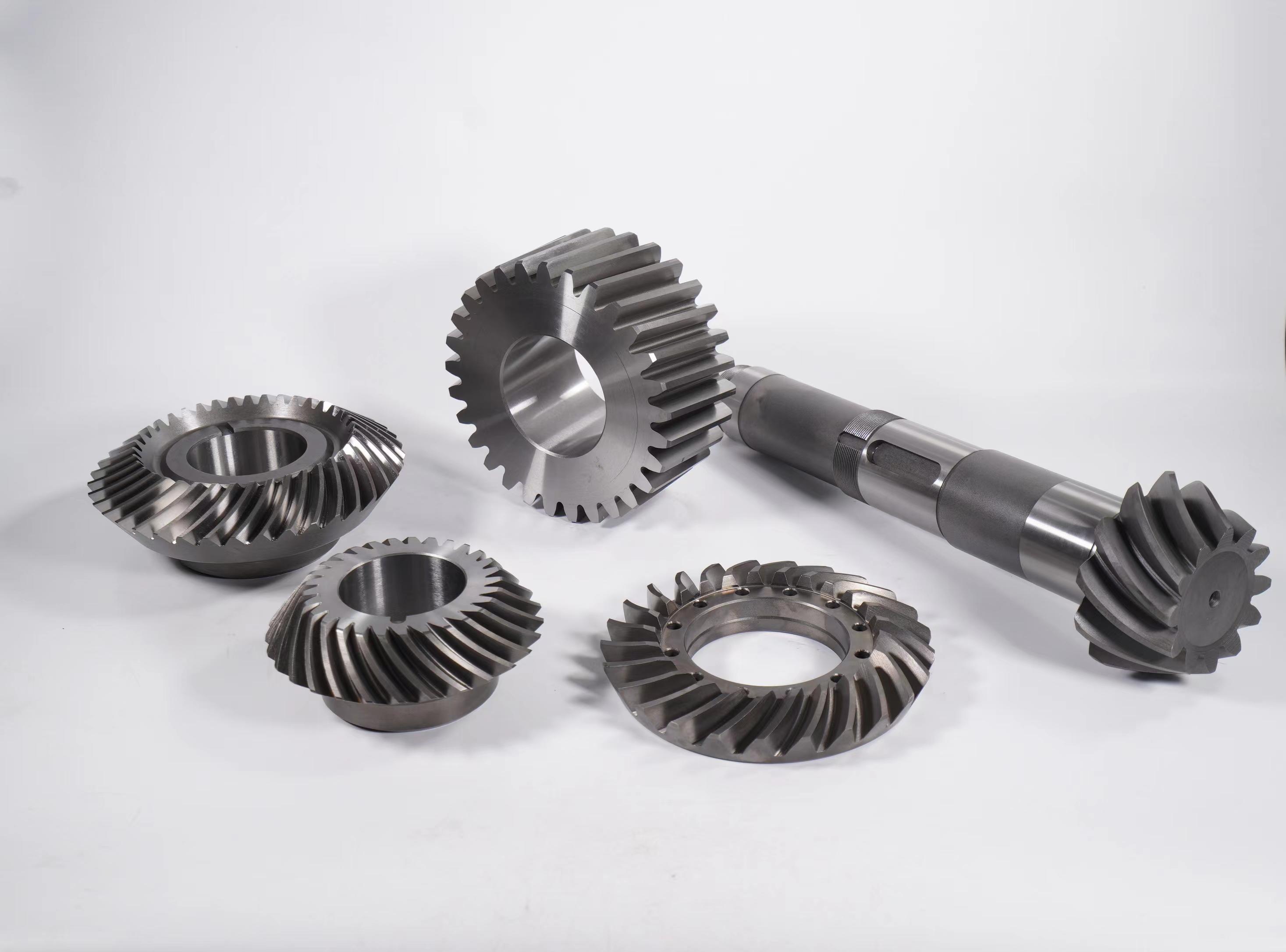
Engranajes cónicos industriales
El engranaje espiral juega un papel importante en la caja de cambios
2. **Perfil y geometría del diente**: Diseñe el perfil del diente del engranaje cónico para garantizar una transmisión eficiente de potencia y un mínimo ruido y vibración. La geometría debe adaptarse al ángulo específico de intersección entre los ejes, que normalmente es de 90 grados para los engranajes cónicos.
3. **Análisis de carga de engranajes cónicos**: Realice un análisis exhaustivo de las cargas esperadas, incluidas las cargas estáticas, dinámicas y de impacto. Considere los efectos de las cargas de choque que pueden ocurrir debido a la acción de las olas o cambios repentinos en el movimiento de la embarcación.
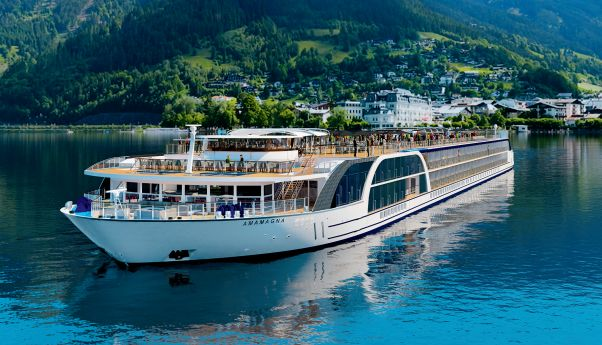
4. **Lubricación**: Diseñe el sistema de engranajes para que cuente con una lubricación adecuada, esencial para reducir el desgaste en entornos marinos. Seleccione lubricantes aptos para uso marino, con propiedades como un alto índice de viscosidad y resistencia a la contaminación por agua.
5. **Sellado y protección**: Incorpora un sellado eficaz para evitar la entrada de agua, sal y otros contaminantes.
Diseñe la carcasa y los compartimentos para proteger los engranajes de los elementos y proporcionar un fácil acceso para el mantenimiento.
6. **Protección contra la corrosión**: Aplique recubrimientos o tratamientos resistentes a la corrosión a los engranajes y componentes asociados. Considere el uso de ánodos de sacrificio o sistemas de protección catódica si los engranajes están en contacto directo con agua de mar.
7. **Confiabilidad y redundancia**: Diseñe el sistema para lograr una alta confiabilidad, considerando factores como la disponibilidad de repuestos y la facilidad de mantenimiento en el mar. En aplicaciones críticas, considere incorporar redundancia para garantizar que el buque pueda seguir operando si falla un conjunto de engranajes.
8. **Simulación y análisis**: Utilice diseño asistido por computadora (CAD) y análisis de elementos finitos (FEA) para simular el rendimiento de los engranajes en diversas condiciones. Analice los patrones de contacto, la distribución del estrés y los modos de falla potenciales para optimizar el diseño.
9. **Pruebas**: Realizar pruebas rigurosas, incluidas pruebas de fatiga, para garantizar que los engranajes puedan soportar la vida útil esperada en condiciones marinas. Probar los engranajes en condiciones marinas simuladas para validar el diseño y la elección de materiales. 10. **Cumplimiento de normas**: Asegurarse de que el diseño cumpla con las normas marinas e industriales pertinentes, como las establecidas por sociedades de clasificación como ABS, DNV o Lloyd's Register.
11. **Consideraciones de mantenimiento**:Diseñe los engranajes para facilitar el mantenimiento, incluidas características que faciliten la inspección, la limpieza y el reemplazo de componentes.
Proporcionar programas y procedimientos de mantenimiento detallados y adaptados al entorno marino.
Al considerar cuidadosamente estos factores durante el proceso de diseño, los engranajes cónicos pueden fabricarse de manera adecuada para el exigente entorno marino, garantizando un rendimiento confiable y duradero.
Hora de publicación: 10 de octubre de 2024